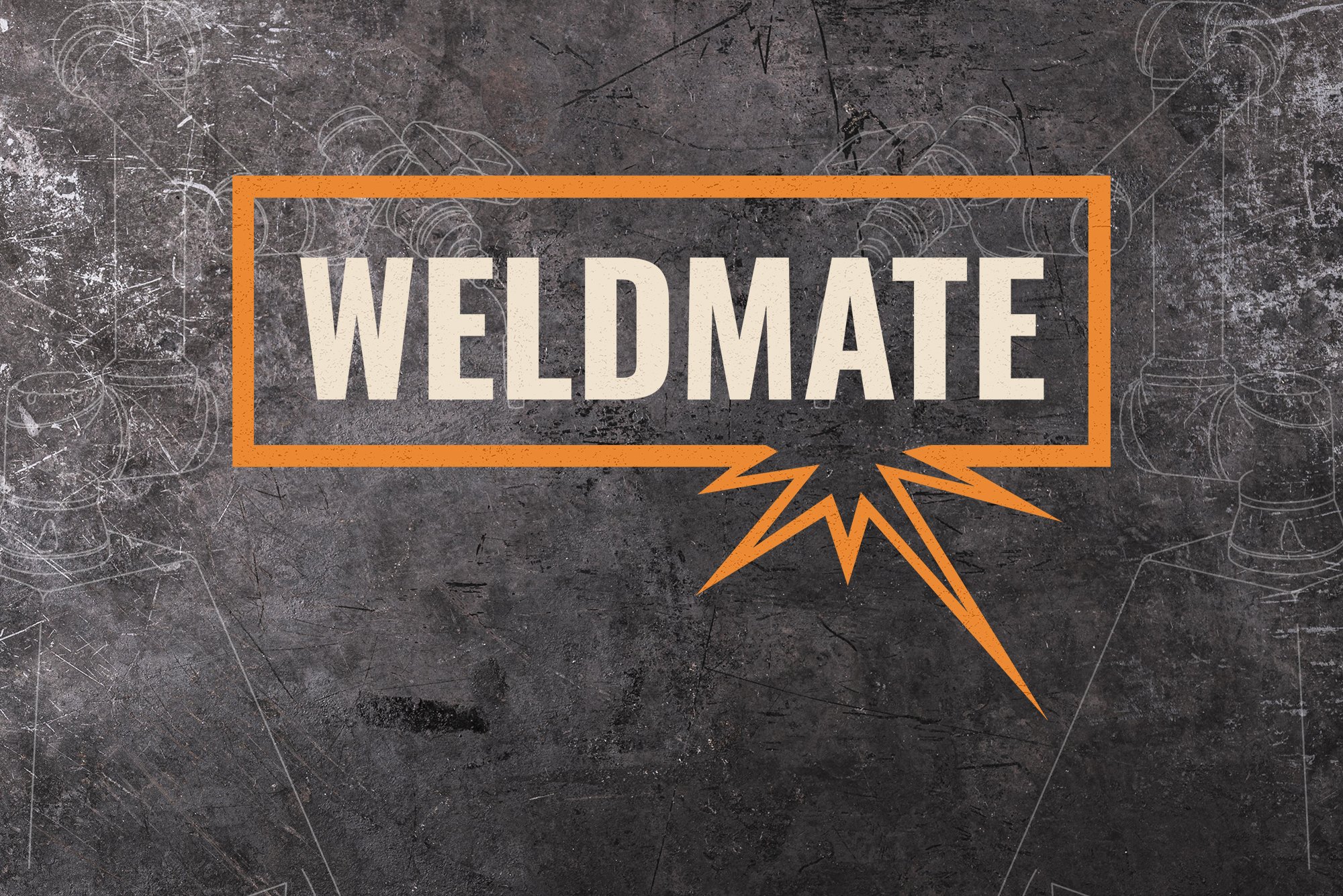
Industrial robotics: our adventure in partnership with german excellence
4 mins read
Harro Höefliger
Harro Höefliger is a world-leading German company specializing in the design and manufacture of production equipment and packaging for a wide range of customers, from the pharmaceutical and medical industries to manufacturers of food, consumer goods and household products. The company’s offering covers all levels of industrialization, while its broad range of services covers the entire product life cycle.
As a technology leader, Harro Höefliger is constantly on the lookout for innovations, even for niche products.
Harro Höfliger offers proven technologies that are perfectly adapted to the specific requirements of each product. For example, pre-measured sachets of dishwasher detergent or washing powder are made from a water-soluble film that is thermoformed and filled with powder, gel or liquid at high speed. Harro Höefliger’s experience in film processing is reflected in every process from feeding to packaging, including forming, dosing, sealing, perforating, punching or die-cutting.
This is the type of process for which Harro Höefliger uses Fuzzy Studio.
The manufacturer was looking for a solution that could quickly and easily generate many digital twins of packaging machine structures from CAD files. These simulations create robot trajectories for inspecting and measuring package layers. The goal is to determine the optimum balance between minimum material thickness and packaging performance. The software also had to be usable by non-experts in robotics programming and integrate with the existing system architecture.
Fuzzy Logic software meets these requirements perfectly.
Testimonial from Jens MARBAZ
Development Engineer- Engineering & Innovation Services – Harro Höefliger
Why did you choose Fuzzy Logic solution ? What does our software bring to Harro Höefliger and what will it change?
As part of a market analysis, I was looking for software that would allow me to visualize a machine structure with a variable robot as a digital twin and to generate a robot program sequence based on the digital twin using a given CAD geometry within this software. In particular, it was necessary to position a measuring device that always moves orthogonally along a path curve at a defined, constant working distance and to generate the corresponding robot program sequence for these curves. The measuring device to be guided by the robot had to be mapped in the digital twin with a special holder, which required a projection of the tool center point within the software.
Other requirements for the software were the ability to handle inputs and outputs and, in particular, to avoid complex programming. Programming should be possible for an employee who does not have in-depth knowledge of robot programming. Furthermore, due to changing CAD geometries, it should be possible to easily exchange the CAD geometries in the software environment by exchanging the CAD model and correspondingly quickly adapt the robot program flow based on the resulting change.
After a technical exchange with the Fuzzy Logic experts, based on my requirements, it quickly became clear that Fuzzy Studio with Fuzzy Real Time Control could meet these requirements using a simple Windows computer and various common industrial robots with MQTT as a universal communication protocol. The rapid integration of the software solution into an existing system architecture using Fuzzy Logic was particularly promising. The most remarkable addition to the system architecture was the integration of the fully preconfigured industrial PC Fuzzy RTOS.
There are similar software solutions on the market, which I had to eliminate in a detailed analysis based on the requirement profile. The reasons for this were :
– The software solution is linked to defined individual robot types (no variability).
– The software solution is designed for welding robots only.
– The software solution requires experience in robot programming.
– The software solution would have had to be adapted to our individual requirements at great expense (no flexibility).
– The software solution would have required specific programming depending on the CAD system and existing data structure.
Fuzzy Logic now allows us to visualize machine structures as a digital twin and to load common robot types into this digital twin. In addition to visualization, process preview, and functions such as collision checking in the digital twin, robot program processes can now be created very quickly and inputs and outputs can be processed to enable an automated process. This is particularly useful for pre-development or laboratory activities that require rapid automation of the robot at an early stage of the project. In addition, it is possible to respond quickly and flexibly to changes in the mechanical structure, which are often necessary in pre-development based on new findings and which normally require complex changes in the robot program sequence. In addition, once the entire system has been jointly commissioned, there is no need for additional personnel from the in-house robotics department to work with the robot and implement changes.
For the programming and automation of the robots in our highly complex machine technology, we do not see fuzzy logic as a suitable all-purpose solution due to its complexity and see the use of our specialists from the relevant department as essential.
Also worth mentioning is the possibility of remote support from Fuzzy Logic. We are very satisfied with Fuzzy Logic’s fast remote support and have been able to avoid on-site visits when problems have arisen. We also find the possibility of updates and extensions within the Fuzzy Studio software package very useful.